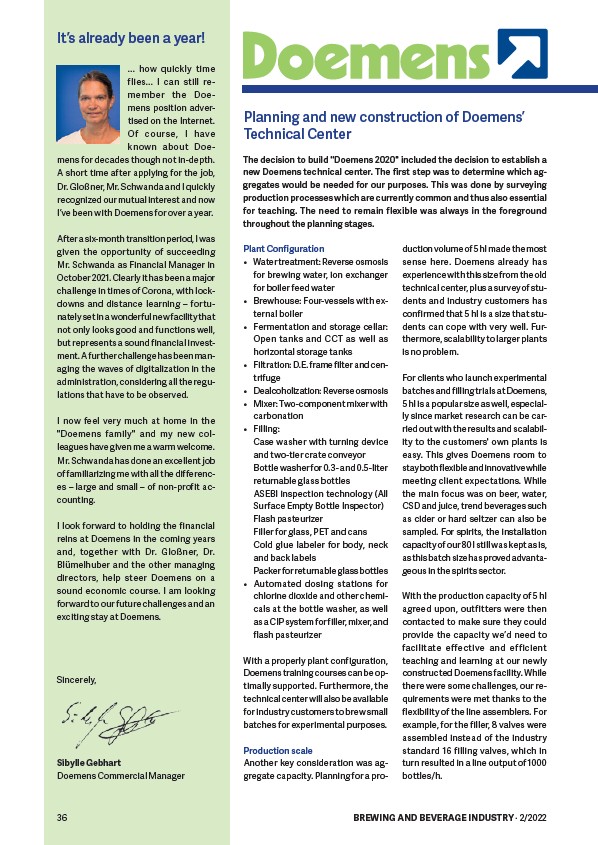
It’s already been a year!
... how quickly time
flies... I can still remember
the Doemens
position advertised
on the Internet.
Of course, I have
known about Doemens
for decades though not in-depth.
A short time after applying for the job,
Dr. Gloßner, Mr. Schwanda and I quickly
recognized our mutual interest and now
I’ve been with Doemens for over a year.
After a six-month transition period, I was
given the opportunity of succeeding
Mr. Schwanda as Financial Manager in
October 2021. Clearly it has been a major
challenge in times of Corona, with lockdowns
and distance learning – fortunately
set in a wonderful new facility that
not only looks good and functions well,
but represents a sound financial investment.
A further challenge has been managing
the waves of digitalization in the
administration, considering all the regulations
that have to be observed.
I now feel very much at home in the
"Doemens family" and my new colleagues
have given me a warm welcome.
Mr. Schwanda has done an excellent job
of familiarizing me with all the differences
– large and small – of non-profit accounting.
I look forward to holding the financial
reins at Doemens in the coming years
and, together with Dr. Gloßner, Dr.
Blümelhuber and the other managing
directors, help steer Doemens on a
sound economic course. I am looking
forward to our future challenges and an
exciting stay at Doemens.
Sincerely,
Sibylle Gebhart
Doemens Commercial Manager
Planning and new construction of Doemens’
Technical Center
The decision to build "Doemens 2020" included the decision to establish a
new Doemens technical center. The first step was to determine which aggregates
would be needed for our purposes. This was done by surveying
production processes which are currently common and thus also essential
for teaching. The need to remain flexible was always in the foreground
throughout the planning stages.
Plant Configuration
• Water treatment: Reverse osmosis
for brewing water, ion exchanger
for boiler feed water
• Brewhouse: Four-vessels with external
boiler
• Fermentation and storage cellar:
Open tanks and CCT as well as
horizontal storage tanks
• Filtration: D.E. frame filter and centrifuge
• Dealcoholization: Reverse osmosis
• Mixer: Two-component mixer with
carbonation
• Filling:
Case washer with turning device
and two-tier crate conveyor
Bottle washer for 0.3- and 0.5-liter
returnable glass bottles
ASEBI inspection technology (All
Surface Empty Bottle Inspector)
Flash pasteurizer
Filler for glass, PET and cans
Cold glue labeler for body, neck
and back labels
Packer for returnable glass bottles
• Automated dosing stations for
chlorine dioxide and other chemicals
at the bottle washer, as well
as a CIP system for filler, mixer, and
flash pasteurizer
With a properly plant configuration,
Doemens training courses can be optimally
supported. Furthermore, the
technical center will also be available
for industry customers to brew small
batches for experimental purposes.
Production scale
Another key consideration was aggregate
capacity. Planning for a pro-
duction volume of 5 hl made the most
sense here. Doemens already has
experience with this size from the old
technical center, plus a survey of students
and industry customers has
confirmed that 5 hl is a size that students
can cope with very well. Furthermore,
scalability to larger plants
is no problem.
For clients who launch experimental
batches and filling trials at Doemens,
5 hl is a popular size as well, especially
since market research can be carried
out with the results and scalability
to the customers' own plants is
easy. This gives Doemens room to
stay both flexible and innovative while
meeting client expectations. While
the main focus was on beer, water,
CSD and juice, trend beverages such
as cider or hard seltzer can also be
sampled. For spirits, the installation
capacity of our 80 l still was kept as is,
as this batch size has proved advantageous
in the spirits sector.
With the production capacity of 5 hl
agreed upon, outfitters were then
contacted to make sure they could
provide the capacity we’d need to
facilitate effective and efficient
teaching and learning at our newly
constructed Doemens facility. While
there were some challenges, our requirements
were met thanks to the
flexibility of the line assemblers. For
example, for the filler, 8 valves were
assembled instead of the industry
standard 16 filling valves, which in
turn resulted in a line output of 1000
bottles/h.
36 BREWING AND BEVERAGE INDUSTRY · 2/2022